Menu
Calcium Aluminate
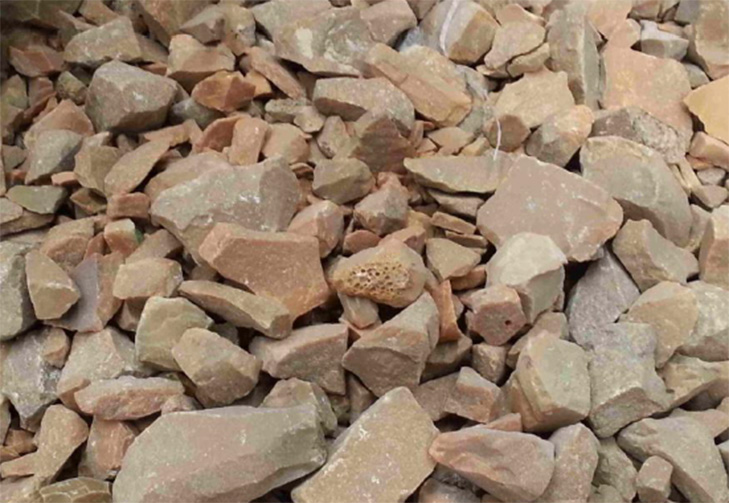
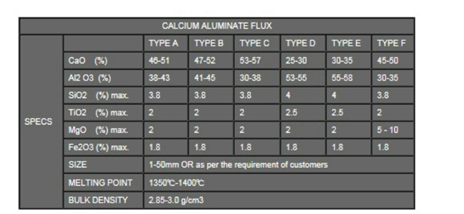
Calcium Aluminate Flux is a kind of auxiliary material for steelmaking. Calcium aluminate flux is made of selected raw material of Calcium and Aluminate, blended at a proper proportion, ground to powder, pelletized after churning, sintered or melted in kiln. The mineral composition of Calcium Aluminate for Synthetic Slag is CA, CA2, C3A and C12A7.
Calcium aluminate flux is used in steel making process specially for desulphurization, dephosphorization and non-metallic inclusion absorption without adversely affecting ladle refractory. Calcium aluminate flux can plays a role of thermal insulation purify liquid steel by preventing steel from reacting with Oxygen, Nitrogen, Hydrogen.calcium aluminate flux is widely used as a steel making addition in most large-scale steel corporation in Japan, USA Chile, and European countries.
Benefits Of Calcium Aluminate Flux
1. Low melting(≤1400℃), low viscosity of melting-slag, optimum fluidity
2. High performance of desulphurization and non-metallic inclusion absorption
3. Energy savings, Ladle refractory protection and the life of ladle prolonging
4. Faster steel refining times and better refining performance
5. Savings on the elimination or reduced consumption, cost effective, production efficient
6. Form slag quickly, avoid moisture absorption, never get powder, environment friendly
Calcium Aluminate Flux can be added into ladle bottom once before slag-removing. The dosage of the calcium aluminate flux will be depended on production on site. The reference dosage is 6-8kg per ton of steel. There is another method. Calcium Aluminate Flux can be added twice, half dosage in ladle bottom at the first time, then put the last with steel flowing. Make sure ventilate at the bottom of ladle. Make the air and slag in steel go up float completely. Keep the steel liquid temperature and chemical composition consistent.